Within the Scarcity Zero framework, Cogeneration Facilities are a flexible deployment of modular systems that function cooperatively to generate both energy and vital resources.
Primary roles of Cogeneration Facilities:
- Generate electricity
- Desalinate seawater into fresh water (Multi-Stage Flash Distillation)
- Extract hydrogen from desalinated seawater (on-site electrolysis)
Secondary roles:
- Employ Direct Air Capture to extract greenhouse gasses from our atmosphere
- Power large-scale waste disposal/recycling through plasma gasification
Tertiary roles:
- Synthesize hydrocarbons through electrolyzed hydrogen and captured CO2 + Methane
- Expand flexibility of synthesized hydrocarbons through gasified syngas
The driving mindset behind this deployment is the ability of technologies to work cooperatively design. Of the many ways this can occur, none are greater than the ability to leverage the waste energy of one technology to help power the functions of another ("cogeneration"). This concept of cogeneration by itself isn't especially new (and is often referred to as "Combined Heat and Power."[1] But it hasn't been a central feature of past power plant design, and has only started to gain prominence relatively recently.[2]
Within the Scarcity Zero framework, cogeneration is maximally sought in all elements of system design. As most power plants today have an efficiency of between 35-50%, half to two-thirds of all of their generated energy is simply written off as "waste heat." Through deliberate systems design, energy-generating technologies can be made to leverage waste heat as much as possible - enabling auxiliary technologies (such as seawater desalination or hydrogen production) to be powered largely if not exclusively by "waste heat" energy alone.
The centerpiece of a Cogeneration Facility is the Small Modular Reactor (SMR), a potent and compact form of power generation that can be mass-manufactured and rapidly deployed as modules. As each SMR is capable of generating 100+ megawatts of power (or greater) and are small enough to be delivered by truck as completely operational units, they allow a Cogeneration Facility’s power generation capacity to be rapidly scaled. Significantly increasing output can be accomplished simply through the delivery of more reactor modules that can be deployed and replaced at will. SMRs are among the most powerful and efficient forms of modular energy generation we have available, and they also output a large volume of heat that can be leveraged to power additional systems. Of these systems, those dedicated to desalinating seawater into fresh water and producing hydrogen through electrolysis take a lead role, but other systems to scrub CO2 from our atmosphere and recycle waste through gasification can be flexibly engaged as well.
The following images illustrate a conceptual deployment of SMR's with other resource-producing systems in a cogenerative capacity that reflects the approach we employ today when building power and resource infrastructure:
But a major problem with this approach is that only the SMR in this design is modular or mass-manufacturable, as most power and resource systems today are each constructed ad-hoc. Unlike most complex technologies within our society today - vehicles, computers, appliances, consumer electronics, even aircraft - power plants are nigh-universally constructed as unique entities that are custom-designed and made to order. Whenever a power plant is constructed, a company or state body hired architects, structural engineers, civil engineers, electrical engineers, environmental engineers, fluid engineers and mechanical engineers to design the plant's functions, then they hired the contractors to build it, the banks to fund it, the insurance companies to underwrite it, the bond companies to back it, the lawyers to sign off on it and the regulators to approve it. And if they wanted to build another, they then had to wipe the slate clean and do it all over again from scratch because the math and materials that worked for plant A didn’t work for plant B.
If you can imagine how expensive cars, televisions or computers would be if they were each custom-designed and made to order by hand - each and every time - it's easy to see constructing power plants can easily cost billions of dollars and take years (if not decades) to complete. This not only limits our power-generating capacity as a society while further limiting our ability to rapidly increase it when required (both as a matter of cost and logistics), it also makes electricity cost far more than necessary and binds electricity as an ultimately scarce resource as opposed to a universal energy source that can be harnessed anywhere on-demand through easily deployable systems that can be flexibly and rapidly reconfigured.
This is the exact result Cogeneration Facilities are intended to achieve. With a first step of integrating cogenerative design within every aspect of power-generating infrastructure, the second step is to design power systems to be mass-manufactured as identical, type-certified product models that are built to a modular standard - meaning they can be swapped and scaled with ease, and come already preconfigured to allow auxiliary resource-production systems to harness their waste energy as a primary power source. As concerns power and resource infrastructure, the idea in abstract is to manufacture them like we manufacture toasters, plug them in like batteries, swap them like we swap lightbulbs, and perform each of the above with the flexibility of plugging in peripheral devices into desktop computer's USB port.
To see what this would look like as a practical example, consider the series of images above that show sample deployments of modular technologies. The first hypothetical deployment (Figure A) extends a power generation capacity of 200 megawatts, a desalination capacity of 1 million gallons (3,785m3) per day, and an electrolysis capacity to produce 423,000 ft2 of compressed hydrogen (1,000kg).
Then, let's assume we needed to increase power generation by 100 megawatts with twice the desalination capacity. As shown by Figure B, it takes all of four truck sorties to deliver another 100 megawatts of power generation, two Multi-Stage Flash Distillation modules at 500K gallon-per-day capacity each, and another modular substation to handle the load generated by the third SMR.
Let us assume thereafter that this location significantly underestimated demand for hydrogen production as well as the volume of excess energy they could devote to atmospheric scrubbing. What would it take to scale their capacity for both by 300%? In this case, six truck deliveries (Figure C).
With this approach, our capacity to generate power or produce resources is completely flexible and indefinitely scalable. Increasing output of either electricity or resources at the same deployment envelope by several times over doesn't take years or decades as it does now. Under this approach, it could be accomplishable in a matter of hours.
This capability is not science fiction. We are readily capable of building systems in this capacity, as we already do in several other economic sectors. Commercial aerospace, for example, shares comparable degrees of precision, technical difficulty and error intolerance as nuclear engineering. Few challenges are more daunting than building systems that annually transport millions of people from rest to 570mph at 36,000 ft. above the Earth – with every single life underwritten by the promise that their aircraft will never fail. Yet today the Boeing corporation can fully assemble its flagship 787 Dreamliner jet every 17 days – less time than it takes Budweiser to brew a bottle of beer.
Power and resource infrastructure can therefore be built the same way under similar performance requirements: rapid, reliable and replicable systems each mass-manufactured to a modular standard. Engaging these capabilities reflects an unprecedented opportunity that can in no way be matched by the current approach we take today to building energy and resource infrastructure, all the more so in the face of significant changes in configuration, output and performance.
We can also accomplish this in other areas of social focus. Of the more severe ecological impacts caused by human activity, the extent of damage to our oceans ranks near the top if not at it. Besides mass overfishing, heavy-metal poisoning and vast destruction of coral reefs, millions of tons of trash float in our seas and accumulate as giant patches that can span thousands of miles.
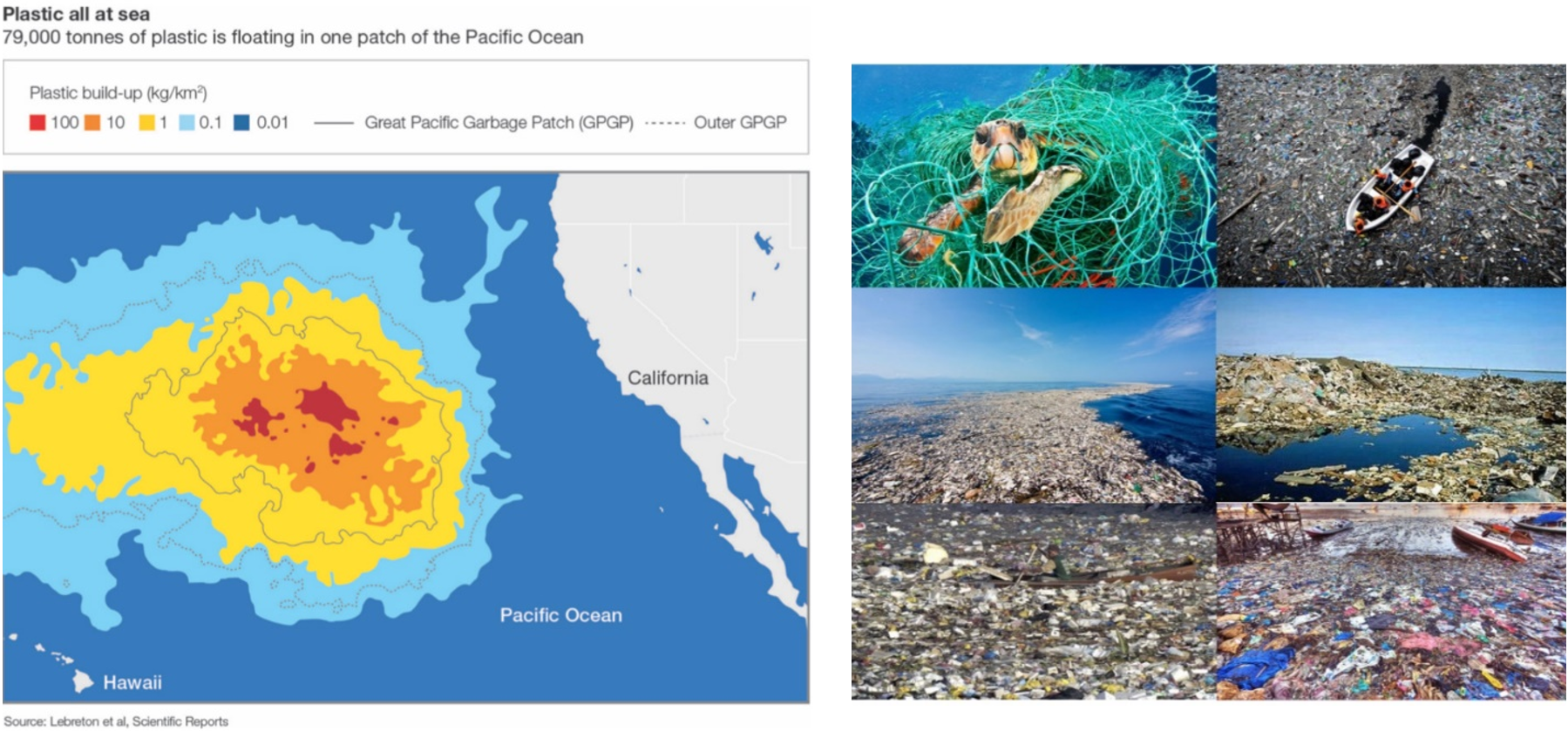
Millions of tons of trash pollute our oceans, destroying our ecology and killing wildlife
Cogenerative deployments of standardized power systems can enable to solve this problem while also manifesting resource abundance. For example, the aforementioned technologies could be deployed at sea with a unique configuration geared for ocean waste processing, seawater desalination and hydrogen production, performing these three roles as a "Trident Facility."
In this concept, Trident Facilities focus equally on mitigating waste as they do produce energy and resources. Not functioning in a dissimilar capacity to an offshore oil rig, Trident Facilities focus equally on producing resources while cleaning ocean trash. Through external waste collection systems (floating sieves for example), trash is brought to the facility where it is hoisted via crane that can lift from either end (or center) of the facility.
While a more significant infrastructural development than Cogeneration Facilities in concept, Trident Facilities demonstrate how cogenerative technology deployments can solve massive problems while serving other roles that are both socially, ecologically and economically beneficial. Thousands of oil rigs float in the oceans today; clearly, this is a system we are capable of building. There is no system currently in service that is capable of serving all of these roles, yet this deployment strategy gives us a singular vector to deploy all of them through a means that can be mass-produced. The same is true of systems that might be dedicated to capturing carbon while producing resources, or any other application where power generation, resource production, ecological cleanup or other energy-intensive task may be required.
Cogeneration, combined with the introduction of modularity, standardization and mass-manufacturing are the critical elements that can enable sophisticated systems to be rapidly deployed in symbiotic operation, and if necessary, reconfigured on demand. It is the final piece of the puzzle necessary to leverage the exponential growth we have achieved in our manufacturing capabilities over the past several decades, and the final step needed to transform our energy and resource paradigm into one of indefinite resource abundance. Combined with Renewable Cities, Cogeneration Facilities present the second component of Scarcity Zero that can drastically increase our capacity for energy generation and resource production. Once implemented at scale, the large volume of desalinated water produced as a dedicated resource sets up the third piece – The National Aqueduct – to complete the core functions of the framework.